Blog
The Brooklyn Bridge: A Marvel of Engineering
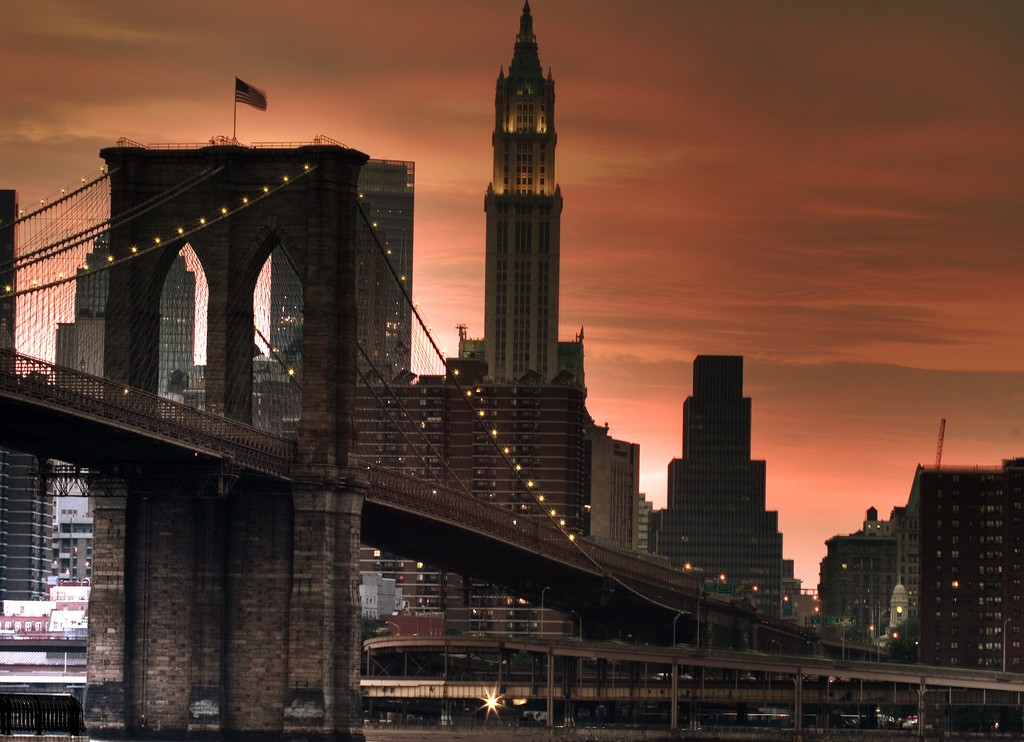
Introduction
The Brooklyn Bridge, completed in 1883, stands as one of the most iconic and revolutionary engineering feats of the 19th century. Spanning the East River to connect Manhattan and Brooklyn, it was the world’s first steel-wire suspension bridge and the longest suspension bridge of its time. For civil engineers, the bridge represents a groundbreaking achievement in structural design, material innovation, and construction techniques that continue to inspire modern infrastructure projects.
This blog post delves into the technical parameters of the Brooklyn Bridge, exploring its structural components, materials, load-bearing mechanisms, and construction challenges. By understanding its engineering brilliance, civil engineers can appreciate the bridge’s historical significance and its lasting influence on suspension bridge design.
1. Historical Context and Design Vision
Before diving into the technical details, it’s essential to understand the bridge’s origins. The Brooklyn Bridge was designed by John Augustus Roebling, a German-born engineer renowned for his expertise in suspension bridge construction. Tragically, Roebling died from an infection before construction began, leaving his son, Washington Roebling, to oversee the project.
Washington Roebling, along with his wife Emily Warren Roebling, managed the construction despite immense challenges, including Washington’s debilitating illness caused by decompression sickness (the “bends”) from working in pressurized caissons.
Key Design Objectives:
- Create a stable, long-span bridge to connect Manhattan and Brooklyn.
- Ensure resilience against wind loads and dynamic forces.
- Accommodate heavy traffic (initially horse-drawn carriages, later automobiles).
- Withstand the corrosive marine environment of the East River.
2. Structural System: Hybrid Suspension & Cable-Stayed Design
The Brooklyn Bridge is often described as a hybrid suspension bridge because it incorporates both suspension cables and diagonal stay cables for added stability. This was a deliberate choice by Roebling to enhance rigidity, as pure suspension bridges of the time were prone to excessive movement.
Main Structural Components:
A. Towers (Pylons)
- Height: 276.5 ft (84.3 m) above high water.
- Material: Limestone, granite, and Rosendale cement (a natural hydraulic cement).
- Foundation: Built on caissons—watertight chambers sunk into the riverbed.
- Manhattan caisson: Reached bedrock at 78 ft (23.7 m) below water.
- Brooklyn caisson: Resting on sand at 44.5 ft (13.6 m) due to softer soil.
- Function: Support the main cables and anchor the bridge’s weight.
B. Suspension Cables
- Material: High-strength steel wire (a revolutionary choice at the time, replacing iron).
- Diameter: 15.75 inches (40 cm) for each main cable.
- Construction: Each cable consists of 5,434 parallel steel wires, bundled into 19 strands.
- Anchorage: Embedded into massive anchorages on both shores, containing 23,000 tons of masonry.
C. Diagonal Stay Cables
- Purpose: Added stiffness to reduce oscillations caused by wind or traffic loads.
- Material: Wrought iron (later reinforced with steel).
- Configuration: Radiate from the towers to the deck, forming a web-like pattern.
D. Deck System
- Width: 85 ft (26 m), accommodating multiple traffic lanes and a pedestrian walkway.
- Material: Timber planks (originally), later replaced with asphalt and steel grating.
- Stiffening Truss: A lattice truss beneath the deck provided additional rigidity.
3. Construction Challenges and Innovations
A. Caisson Foundations: A Pioneering Feat
Building the bridge’s foundations required working in pressurized caissons, a dangerous and unprecedented technique. Workers (called “sandhogs”) excavated riverbed material while compressed air kept water out.
- Decompression Sickness (“The Bends”): Many workers, including Washington Roebling, suffered from this condition due to rapid pressure changes.
- Innovation: Despite the risks, the caissons successfully reached stable ground, setting a precedent for deep foundation engineering.
B. Cable Spinning Technique
Roebling adopted a wire-by-wire spinning method, where individual steel wires were looped across the river and compacted into cables.
- Precision Required: Each wire had to be tensioned uniformly to ensure load distribution.
- Quality Control: Workers meticulously inspected wires for defects, a practice that influenced modern cable manufacturing.
C. Wind and Dynamic Load Considerations
The collapse of other suspension bridges (like the Wheeling Suspension Bridge in 1854) due to wind-induced vibrations prompted Roebling to incorporate stiffening trusses and stay cables.
- Aerodynamic Stability: The hybrid design reduced susceptibility to flutter and torsional oscillations.
- Lessons for Future Bridges: The Tacoma Narrows Bridge failure (1940) later reinforced the importance of aerodynamic testing, validating Roebling’s cautious approach.
4. Load-Bearing Capacity and Structural Analysis
A. Dead Load vs. Live Load
- Dead Load (Self-Weight): ~14,680 tons (including cables, deck, and towers).
- Original Live Load Capacity: Designed for horse-drawn carriages (~3.4 kN/m²).
- Modern Reinforcement: Strengthened over the years to handle vehicular traffic (~18.6 kN/m²).
B. Cable Tension and Force Distribution
- Main Cables: Each carries approximately 11,200 tons of tension.
- Anchorages: Resist horizontal forces by transferring tension into the bedrock.
- Stay Cables: Provide additional load paths, reducing stress on the main suspension system.
C. Deflection and Dynamic Response
- Maximum Deflection: Under full load, the deck deflects ~3 ft (0.9 m), well within safe limits.
- Natural Frequency: Engineered to avoid resonance with wind or pedestrian-induced vibrations.
5. Material Innovations and Durability
A. Transition from Wrought Iron to Steel
- Early Suspension Bridges: Used wrought iron, which was weaker and prone to corrosion.
- Roebling’s Choice: Opted for steel wire, which had higher tensile strength (about 160 ksi vs. wrought iron’s 40 ksi).
B. Corrosion Protection
- Galvanized Steel Wires: Coated with zinc to resist rust.
- Regular Maintenance: Inspections and re-tensioning ensure longevity.
C. Masonry and Mortar Durability
- Rosendale Cement: A natural hydraulic cement that hardens underwater, crucial for the caissons.
- Granite Facing: Provides erosion resistance against the East River’s tidal forces.
6. Legacy and Lessons for Modern Civil Engineers
The Brooklyn Bridge remains a testament to visionary engineering. Key takeaways for today’s civil engineers include:
- Hybrid Structural Systems – Combining suspension and cable-stayed elements can enhance stability.
- Deep Foundation Techniques – Caisson construction paved the way for modern skyscrapers and underwater tunnels.
- Material Advancements – The shift from iron to steel revolutionized bridge design.
- Resilience Against Dynamic Loads – Aerodynamic considerations are critical for long-span bridges.
- Long-Term Maintenance – Proper inspection and upkeep ensure centuries of service.
Conclusion
The Brooklyn Bridge is more than just a historic landmark—it’s a masterclass in civil engineering. From its innovative hybrid suspension system to its pioneering use of steel and caisson foundations, every aspect of its design reflects meticulous planning and bold execution.
For modern engineers, studying the Brooklyn Bridge offers invaluable insights into load distribution, material selection, and structural resilience. As suspension bridges continue to evolve (think of the Golden Gate Bridge or Japan’s Akashi Kaikyō Bridge), Roebling’s masterpiece remains a foundational reference in the annals of engineering history.
Whether you’re a student, a practicing engineer, or simply an admirer of great infrastructure, the Brooklyn Bridge stands as a reminder that visionary engineering can defy the limits of its time—and endure for generations.